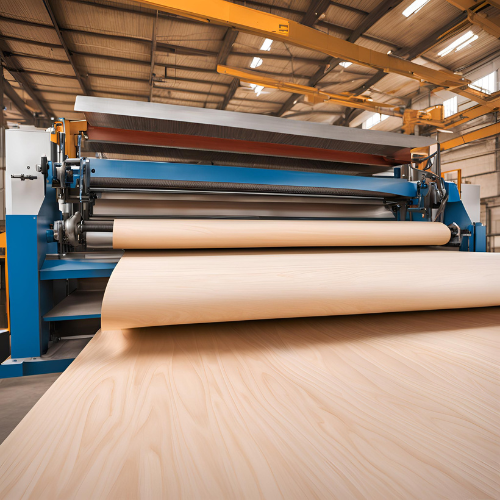
Understanding Rubber Roller Wear
Rubber rollers are essential components in various industrial applications, contributing significantly to efficiency and productivity. Despite their durability, they are not impervious to wear and degradation over time. Understanding the factors contributing to rubber roller wear is crucial for maintaining industrial roller lifespan and ensuring optimal performance. Various elements can accelerate the wear process, leading to unexpected downtime and increased operational costs.
One primary reason for rubber roller degradation is the material’s inherent exposure to harsh conditions, including temperature fluctuations, chemical interactions, and mechanical stresses. Factors such as friction, misalignment, and improper loading can exacerbate wear, causing surface deterioration that impacts functionality. Additionally, environmental elements such as humidity and UV radiation can weaken the rubber compound, contributing to premature failure.
Identifying the common causes of wear allows operators and maintenance teams to implement proactive roller maintenance tips designed to mitigate degradation. Regular inspections play a vital role in early detection of wear patterns, enabling timely repairs or replacements. Moreover, employing proper cleaning techniques and protective coatings can prolong the lifespan of rubber rollers, reducing the frequency of replacements and enhancing overall efficiency.
Furthermore, understanding the application-specific performance requirements is essential for selecting the right rubber compounds tailored to withstand unique operating conditions. Each industrial setting may demand different characteristics from its rubber rollers, which makes careful consideration of material selection critical to performance sustainability.
By addressing these factors and committing to regular maintenance practices, businesses can significantly reduce the risk of rubber roller wear, optimize industrial roller lifespan, and ultimately boost operational reliability. This proactive approach is essential for fostering efficiency and cost-effectiveness in integrated manufacturing processes.
Common Causes of Rubber Roller Wear
Rubber rollers play a crucial role in various industrial applications, yet they are susceptible to wear and degradation over time. Understanding the common causes of rubber roller wear can assist in implementing effective rubber roller wear prevention strategies, ensuring longevity and optimal performance.
One of the primary factors contributing to rubber roller degradation is excessive heat. High temperatures can deteriorate the rubber compounds, leading to loss of elasticity and brittleness. For instance, in printing or laminating processes where rollers are exposed to consistent heat, the resulting thermal stress can significantly reduce the industrial roller lifespan. Regular monitoring of temperature levels and ensuring adequate cooling measures can help mitigate this issue.
Chemical exposure also poses a substantial threat to rubber rollers. Certain chemicals, including solvents and acids, can interact adversely with rubber materials, resulting in swelling, discoloration, or cracking. For example, rollers that encounter inks or other production fluids may experience varying degrees of degradation, depending on the chemical composition. It is vital to understand the material compatibility when selecting rollers for operations to prevent premature wear.
Additionally, abrasion is another significant cause of wear. Friction and surface contact between rubber rollers and other materials can lead to gradual material removal, ultimately resulting in reduced performance. This can be particularly prevalent in environments where rollers are used against rough surfaces or when debris accumulates. Employing protective measures, such as regular cleaning and using abrasion-resistant materials, can be beneficial.
Finally, incorrect pressure settings can lead to uneven wear patterns on rubber rollers. Insufficient or excessive load configurations may cause localized stresses that impact the roller’s integrity, thereby compromising its effectiveness. It is essential to maintain proper pressure settings based on the operational requirements to enhance roller maintenance and extend their lifespan significantly.
Prevention Strategies for Rubber Roller Wear
Effective prevention strategies for rubber roller wear are essential to maintain the optimal performance and longevity of industrial rollers. One of the fundamental approaches is conducting regular maintenance checks. These checks allow operators to identify signs of wear early, enabling timely interventions that can mitigate further degradation. Regularly scheduled inspections should focus on assessing the condition of the rubber surface, checking for cracks, and ensuring that the roller is operating within the appropriate temperature range. By addressing minor issues promptly, facilities can significantly reduce the overall wear and extend the industrial roller lifespan.
Another key factor in rubber roller wear prevention is selecting the appropriate rubber materials suited for specific applications. Different industries have varying demands that require distinct rubber compositions. For instance, rubber formulations can be adjusted to enhance resistance against abrasion, heat, or chemicals, thereby directly impacting roller maintenance. By choosing materials that withstand the operational environment, companies can mitigate the risk of rubber roller degradation. Engaging with suppliers who understand the unique challenges of each application will help in identifying the most suitable materials.
Moreover, utilizing protective coatings or sleeves is advantageous for shielding rollers from adverse conditions. These protective barriers can prevent direct wear caused by contact with other surfaces or exposure to harsh chemicals. Coatings can also enhance the durability of rollers by providing an additional layer of defense against thermal and mechanical stress. When implementing these strategies, it is vital to ensure that the protective materials used do not interfere with the roller’s functionality or the quality of the finished product. By integrating these prevention strategies, industries can effectively manage rubber roller wear and ensure consistent operational performance.
Maintenance Best Practices
Maintaining rubber rollers is essential for ensuring their longevity and optimizing their performance in various industrial applications. Effective rubber roller wear prevention strategies begin with proper cleaning techniques. Regularly removing dirt, dust, and debris from the surface can significantly reduce the potential for rubber roller degradation. It is advisable to use a soft brush or cloth along with a mild detergent to maintain cleanliness without damaging the rubber material itself. Furthermore, avoiding abrasive cleaners will help preserve the integrity of the roller surface, which plays a crucial role in maintaining its functionality.
When rubber rollers are not in use, proper storage techniques should be implemented. It is essential to store rollers in a cool, dry environment away from direct sunlight and extreme temperatures, as these factors can contribute to premature degradation. Additionally, using protective coverings or wrapping rollers in a breathable material can further prevent dust accumulation and potential physical damage.
Another critical aspect of roller maintenance involves conducting regular inspections. Schedule routine checks to identify early signs of wear, such as cracks, uneven surfaces, or discoloration. Detecting these issues promptly can help avert extensive damage and costly production disruptions. Should any irregularities be found, consider taking the necessary steps for repair or replacement. Proactive replacement of worn-out rollers is not merely a recommendation; it is vital for extending the industrial roller lifespan and ensuring continuous operation without compromising product quality.
By incorporating these roller maintenance tips into a comprehensive maintenance plan, facility owners can significantly enhance the efficiency of their rubber rollers, thereby minimizing downtime and boosting overall productivity. The integration of these best practices into daily operations will provide a solid foundation for effective rubber roller wear prevention and optimal performance in industrial settings.