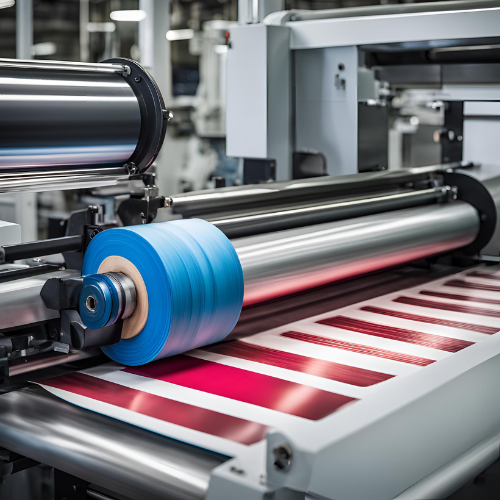
The Evolution of Rubber Rollers in Manufacturing
The history of rubber rollers in manufacturing dates back to the early 19th century, when the introduction of rubber as a material revolutionized multiple industries. Initially, rubber was primarily used for basic applications such as tires and gaskets. However, as manufacturing processes advanced, the potential of rubber rollers began to be recognized. These rollers were initially produced with natural rubber, offering limited flexibility and durability. As time progressed, the industry witnessed a shift towards synthetic rubber, which vastly improved the performance characteristics of rubber rollers in various applications.
Throughout the 20th century, significant advancements in rubber technology and material science contributed to the evolution of rubber rollers. The introduction of various elastomers and additives allowed for the creation of rollers that could withstand challenging environments and enhance operational efficiency. This progression not only improved the longevity of the rollers but also expanded their applications within the manufacturing sector. For instance, modern rubber roller applications now include the printing, paper, and textile industries, where consistent pressure and precision are paramount.
The versatility of rubber rollers has allowed them to adapt and thrive in an ever-changing industrial landscape. Innovations in rubber roller technology have led to the development of rollers that can operate effectively across diverse temperature ranges, resist wear and tear, and minimize noise during operation. As industries seek to enhance their manufacturing processes, the integration of rubber rollers has proven indispensable, facilitating smooth material handling and increasing overall productivity.
In the contemporary manufacturing environment, rubber rollers are an essential component, contributing to automation and efficiency. The evolution of these rollers from basic tools to advanced manufacturing solutions highlights their foundational role and adaptability in meeting the demands of modern manufacturing. Their ongoing development suggests that innovative rubber roller uses will continue to expand, fostering new applications and improving existing processes.
High-Precision Printing: Enhancing Quality and Efficiency
In the realm of modern manufacturing, high-precision printing stands as a vital process, particularly as industries aim for accuracy and quality in their products. Innovative rubber roller uses have drastically transformed this segment by enhancing both the quality and efficiency of print operations. These rollers are designed with precision-engineered surfaces that provide superior grip and reliability, which is critical in minimizing print errors and ensuring that output consistently meets stringent quality standards.
The evolution of rubber roller technology has enabled the development of specialized rollers that cater specifically to the diverse needs of high-precision printing. The materials and designs have been optimized to reduce smudging and maintain uniform ink application. This level of detail is beneficial for a range of industries, including packaging, textiles, and commercial printing. For instance, the packaging industry relies significantly on high-quality print output for branding and information delivery, where even minor inaccuracies can lead to major setbacks in marketing and compliance.
Case studies have demonstrated how modern rubber roller applications can drastically improve output quality and efficiency. In a recent scenario involving a large commercial printer, the integration of advanced rubber rollers led to a 20% reduction in waste due to faulty prints, translating into significant cost savings. Additionally, the implementation of these rollers has resulted in faster turnaround times for clients, showing a direct link between the adoption of innovative roller technology and improved business performance.
As manufacturing continues to evolve, the role of rubber rollers in high-precision printing will likely expand, with ongoing innovations further enhancing their capabilities. By addressing the need for reliability and quality, rubber rollers will remain an integral part of the printing process, enabling industries to achieve their goals in a competitive marketplace.
FDA-Approved Rubber Rollers in Food Processing
The food processing industry relies heavily on various technologies to ensure safety, efficiency, and preservation of food products. An essential component of this industry is the use of rubber rollers, which have become increasingly important due to their compliance with FDA regulations. FDA-approved rubber rollers are specifically designed for applications that come into direct contact with food, ensuring that safety standards are met throughout the manufacturing process.
The primary role of rubber rollers in manufacturing for food processing includes tasks such as conveying, packaging, and forming products. These rollers are often made from high-quality, food-grade materials that minimize the risk of contamination. For instance, silicone rubber rollers are frequently utilized due to their resistance to heat and chemical deterioration, providing an added layer of safety. Additionally, the smooth surface of these rollers aids in maintaining product integrity, reducing the likelihood of food damage during handling.
Innovative rubber roller uses have emerged to enhance hygiene and cleanliness throughout production lines. For example, specialized roller coatings have been developed that prevent microbial growth, significantly improving food safety. Furthermore, modern rubber roller applications often incorporate technologies that enable easy cleaning and maintenance, which is paramount in food processing environments where sanitation is crucial.
Rubber roller technology has evolved to meet the demands of a fast-paced food industry. Advanced manufacturing techniques enable the production of rollers that are not only durable and resistant to wear but also customizable to fit specific production needs. These innovations have allowed companies to optimize their operations, reduce waste, and ultimately deliver safe products to consumers efficiently. The critical role of FDA-approved rubber rollers in food processing cannot be overstated, as they ensure compliance with safety standards while facilitating essential manufacturing processes. In conclusion, the integration of these components is vital for maintaining product quality and safety in the food processing sector.
High-Stakes Applications: Medical Device Manufacturing and Automotive Industries
In the realm of modern manufacturing, rubber rollers have emerged as pivotal components, especially within high-stakes industries such as medical device manufacturing and automotive production. The stakes are considerably higher in medical device manufacturing, where the precision of each product can directly influence patient safety and health outcomes. In such highly regulated environments, rubber rollers are employed to handle delicate materials with utmost care while maintaining sterile conditions. The use of innovative rubber roller technology ensures that devices such as syringes, catheters, and surgical instruments are produced with impeccable accuracy, adhering to stringent specifications. The materials used in rubber rollers are selected for their ability to withstand chemical exposure and environmental stresses, thereby minimizing contamination risks.
Conversely, in the automotive sector, rubber rollers are integral to the fabrication of a variety of essential components, including windshields, tires, and interior fittings. The automotive industry demands a broader focus on durability and quality, making rubber rollers an indispensable asset in assembly lines. They are utilized in processes such as die-cutting and extrusion, where the precision of rubber rollers is critical to ensure that components meet the high standards expected by consumers. The modern rubber roller applications in the automotive sector leverage advancements in material science, which have led to the development of specialized rubber compounds that enhance resilience and performance under stress.
Both industries highlight the versatility of rubber rollers and their vital role in maintaining quality control. Their ability to provide consistent pressure and support during manufacturing processes directly contributes to the overall efficiency and reliability of production. As manufacturing continues to evolve, the integration of innovative rubber roller uses will likely expand, further enhancing the potential of technology in these vital sectors.